Future of 3D printing: Exploring the impact of organic raw filaments on sustainability
- Joan Ubide
- Jun 26, 2024
- 4 min read
Updated: Jul 1, 2024
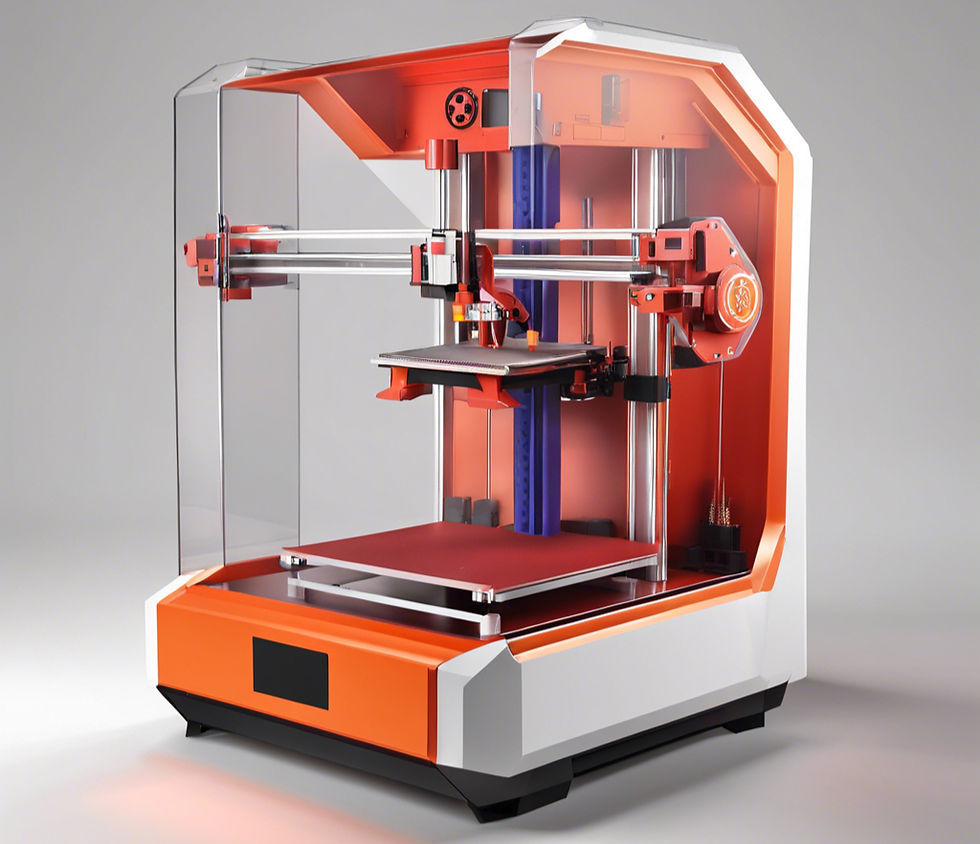
Innovators hold differing opinions on plastic packaging. It is an accessible option that benefits corporate resilience and customer affordability. However, microplastics pollute oceans, impact human health, and exacerbate climate change. Advancements in 3D printing may now enable a balance between plastic's advantages and eco-conscious compositions.
Defining sustainable packaging
The term 'sustainable' in packaging lacks strict regulation. 3D printing could influence this area by providing clearer definitions. Most manufacturers and governments do not strictly define eco-friendly containers, but 3D-printed prototypes offer innovators a clearer understanding of sustainable packaging.
Early adopters of 3D-printed packaging seek third parties to certify their carbon commitments. Organisations such as the Carbon Disclosure Project and Ecovadis evaluate the material origins and ethical working environments of these new production methods. This promotes a shift towards standardised, sustainable manufacturing practices. 3D printers use less energy than conventional production lines, and smarter material utilisation saves companies significant resources and time.
Using conscious, flexible materials
Plastic is wasteful and its high consumption is evident in landfills and waterways. 3D printing can address this issue by creating materials using biodegradable, nature-based ingredients. Moulded fibres, wood pulps, and bio-based resins are popular options compatible with injection moulding methods and modern 3D printing machinery. These greener materials also prevent waste in prototyping and production.
However, using nature-based materials is not sufficient. Companies must also reduce their overall material usage to be more mindful of resource consumption. Reducing material and waste is a notable packaging trend due to its numerous advantages across the entire value chain. Manufacturers can further reduce production waste by using custom moulds. 3D printing allows for the construction of most shapes, resulting in thinner, more form-fitting packaging that weighs less during shipping, thereby saving fuel and reducing carbon emissions.
The evolution
The evolution of 3D printers using organic raw filament is a fascinating journey marked by significant technological advancements and a growing emphasis on sustainability. Here’s a detailed look at this evolution:
Early development and initial use
1980s-1990s: Birth of 3D Printing Technology
Stereolithography (SLA): Invented by Chuck Hull in 1986, SLA was the first form of 3D printing but used photopolymer resin rather than organic materials.
Fused Deposition Modeling (FDM): Developed by S. Scott Crump in 1989, FDM used thermoplastic materials and laid the groundwork for later adaptations involving organic filaments.
Introduction of organic filaments
2000s: Growing awareness of sustainability
Polylactic Acid (PLA): A breakthrough in the early 2000s, PLA is derived from renewable resources like corn starch or sugarcane. It became the first widely adopted organic filament, known for its biodegradability and low environmental impact.
Research and Development: Universities and companies began exploring other organic materials to reduce reliance on petroleum-based plastics.
Advancements in organic filament technology
2010s: Diversification and innovation
Blended Filaments: Manufacturers started blending PLA with other organic materials such as wood, bamboo, and coffee grounds, producing filaments with unique textures and appearances.
Advanced Composites: The development of composite filaments combining PLA with carbon fibre, hemp, or algae to enhance mechanical properties while maintaining environmental benefits.
Commercial Availability: The market for organic filaments expanded, with companies like ColorFabb, Proto-pasta, and Filabot leading the way in providing diverse and high-quality options.
Modern era: Enhanced capabilities and sustainability
2020s: Technological Maturation and Eco-Friendliness
Biodegradable Polymers: Continued refinement of PLA and the development of new biodegradable polymers, such as Polyhydroxyalkanoates (PHA), offering improved performance and environmental benefits.
Recycled Filaments: The introduction of filaments made from recycled organic materials, including post-consumer waste and industrial by-products, promoting circular economy principles.
Functional Applications: Organic filaments are increasingly used in functional and end-use parts, not just prototypes, in industries like fashion, automotive, and consumer goods.
Future prospects
2024 and beyond: Sustainability and innovation
Bio-based nanocomposites: Research is focusing on integrating nanomaterials with organic polymers to create bio-based nanocomposites with superior strength, durability, and functionality.
Sustainable manufacturing: The industry is moving towards more sustainable manufacturing processes, including the use of renewable energy sources and closed-loop recycling systems for filament production.
Expanded material library: Ongoing exploration of new organic sources, such as chitin, silk, and cellulose, could further diversify the range of 3D printing materials available.
Impact on industries
Prototyping and design: Designers and engineers benefit from the eco-friendly properties of organic filaments for rapid prototyping and product development.
Healthcare: Biocompatible and biodegradable filaments open new possibilities in medical applications, including custom implants, prosthetics, and scaffolds for tissue engineering.
Education and maker communities: Organic filaments provide a safe, non-toxic option for educational settings and hobbyists, promoting creativity and sustainability.
The evolution of 3D printers using organic raw filament reflects a broader trend towards sustainable manufacturing and material innovation. From early experiments with PLA to advanced bio-based composites, this technology continues to evolve, offering environmentally friendly alternatives without compromising performance and functionality.
The evolution of 3D printers using organic raw filament highlights a significant advancement in sustainable manufacturing, directly aligning with UN Global Goal 9: Industry, Innovation, and Infrastructure.
By integrating organic raw filaments, the 3D printing industry not only supports sustainable production practices but also fosters material innovation. This shift promotes efficient resource utilization and the development of resilient infrastructure, core components of Goal 9. As the technology continues to evolve, it promises further contributions to a greener, more sustainable industrial landscape.
Sources: https://www.innovatorsmag.com/can-new-3d-printing-options-tackle-scourge-of-plastic-pollution/
Youtube credits: https://www.youtube.com/@3DRevolution